Use cases
With a modular and scalable architecture powered by the Robot Operating System (ROS), ACROBA revolutionizes the automation of complex manufacturing processes by reducing human intervention while maintaining unparalleled precision, adaptability, and adherence to stringent safety and regulatory standards.
The ACROBA solution has undergone rigorous testing in real world industrial settings and has been successfully deployed across five distinct pilot lines. Each pilot line addresses specific challenges, demonstrating the versatility and robustness of the ACROBA system in diverse industrial contexts.
Below, we explore the 5 ACROBA pilot lines and their contributions to the robotics landscape.
Automation of a 3D printing process line for medical device manufacturing (STERIPACK, Ireland)
Plastic Manufacturing Pilot Lines for large part finishing (CABKA/MOSES)
Electric Components Assembly Pilot Line for electric motors manufacturing (ICPE)
Electronic Elements Assembly Pilot Line for electronic circuits production (IKOR)
Lights out pilot lines
The lights out pilot lines align with the overarching goals of the ACROBA project, which aim to develop and demonstrate AI-driven, cognitive robotic platforms tailored to agile production environments. By integrating cutting-edge robotics, safety compliance measures, and user-friendly interfaces, these use cases establish a blueprint for deploying autonomous systems in customizable and scalable manufacturing processes while utilizing the ACROBA platform.
Automation of a 3D printing process line for medical device manufacturing
(Ireland)
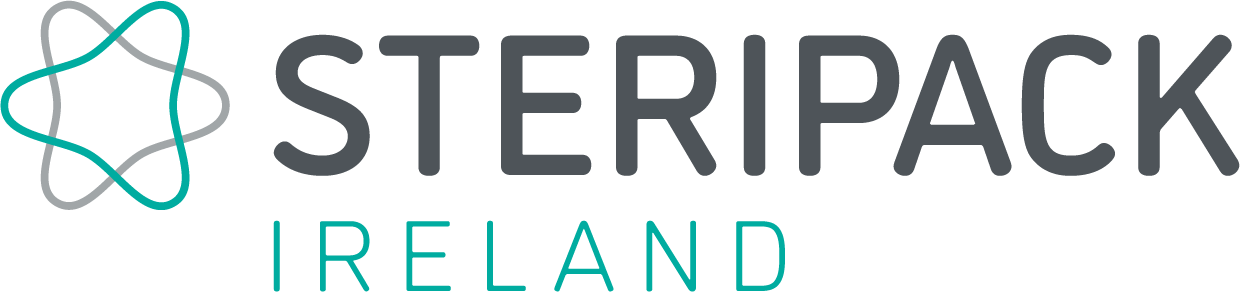
STERIPACK is a contract manufacturer of medical devices offering tailor-made production solutions designed to meet the highest industry standards.
The pilot project focuses on automating a 3D printing production line. The process incorporates an advanced robotic system powered by the ACROBA platform, managing both pre-processing and post-processing tasks integral to the 3D printing workflow. Prior to automation, these tasks were performed manually.
The primary goal is to minimize human intervention by automating critical stages of the process, such as part cleaning, part removal, and support structure removal. Using the ACROBA system, these tasks are executed by robots equipped with generic skills and commercially available hardware.
This approach enhances efficiency, reliability, and safety while reducing the need for constant operator oversight.
The automated line operates seamlessly from start to finish, beginning with the input of a 3D CAD file and concluding with the final inspection of the produced component. The system ensures a streamlined, end-to-end solution.
The manufacturing of large size plastic components involves technical challenges which usually result on the generation of defects in the products which require further reprocessing. The ACROBA solution has been successfully tested on two use cases related to plastic parts manufacturing :
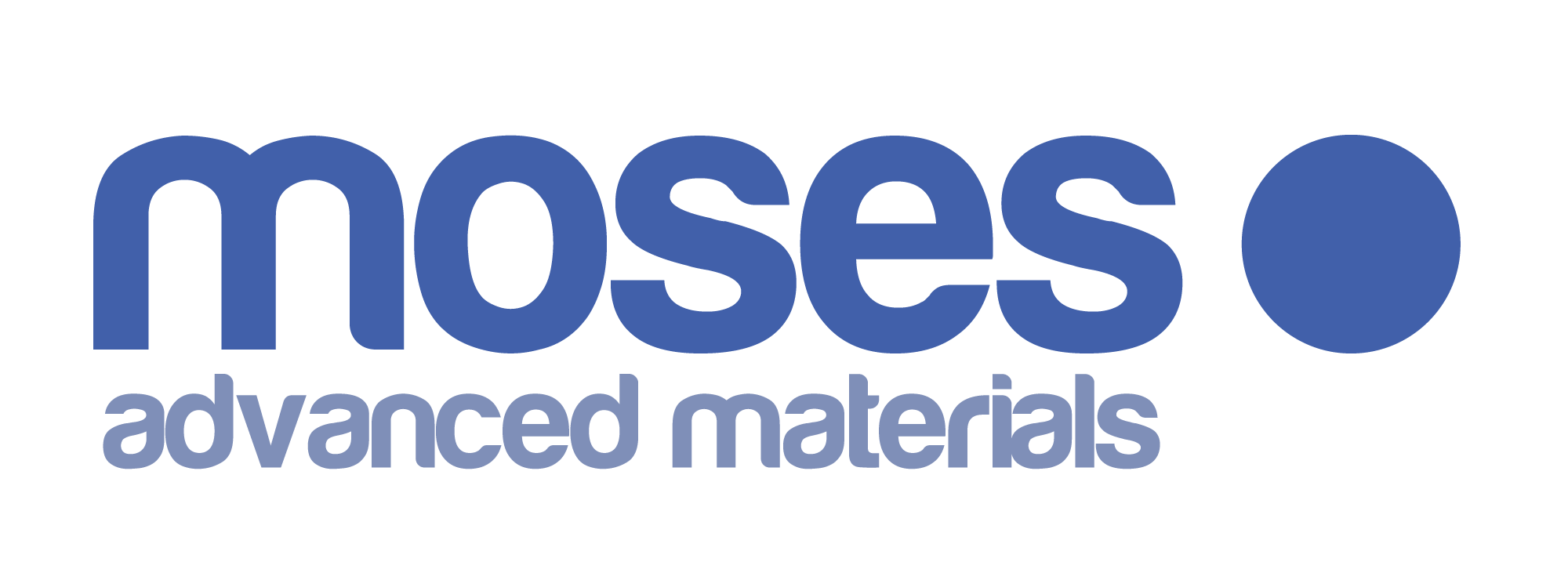
CUSTOMIZATION OF LARGE CONTAINER LIDS
MOSES is expert in the transformation of Fossilbased, Biobased and Biodegradable materials. One of its main activity focuses on the production of customized plastic parts.
The pilot project focuses on the customization of large container lids for urban areas. Their production requires deburring before their commercialisation, a process that is difficult to automatise. The integration of the ACROBA platform enabled MOSES to act across the entire value chain of the plastic parts customization process including:
- Creation of trajectories
- Calibration of the robot, tools and cell
- Execution of the robotic process
As a result, MOSES has now a flexible robotic cell capable of making precise cuts and drills, while generating trajectories quickly and accurately.
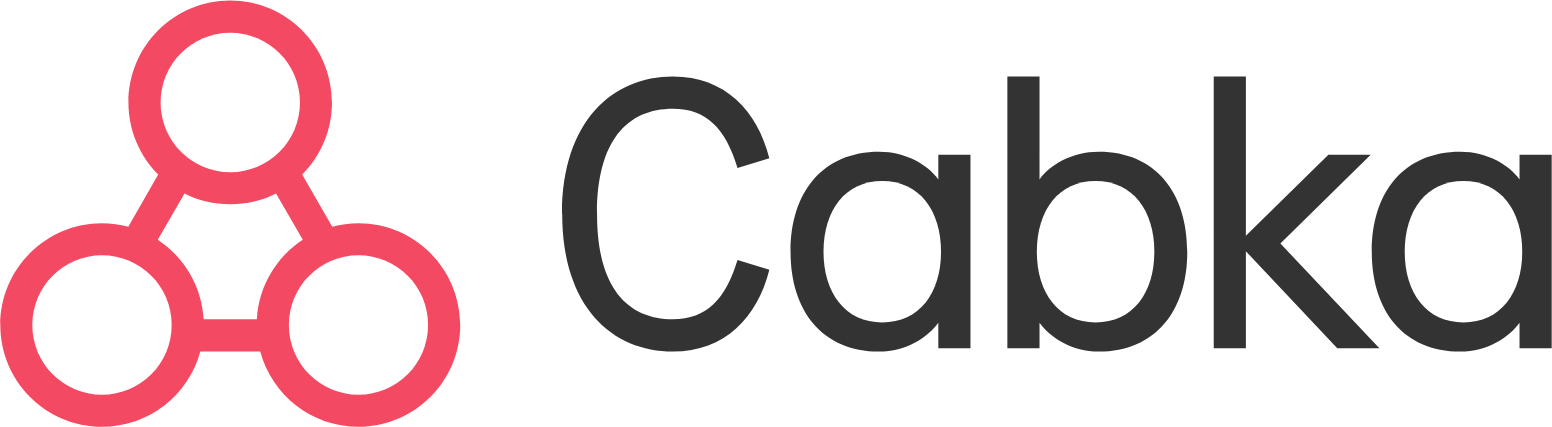
DEBURRING PLASTIC PALLETS
CABKA is a manufacturer of technical plastic products including plastic pallets.
The production process for plastic pallets involves flash defects caused by high injection pressures that must be deburred mechanically to meet the required quality standards. The current process is performed entirely manually by an operator. This meticulous operation requires significant time and human resources. The pilot project aims to automate this manual deburring process. ACROBA is used to :
- Detect defects in injected pallets
- Automatically remove flashes
Plastic Manufacturing PLs for large part finishing
(SPAIN)
Collaborative assembly pilot lines
Collaborative assembly refers to a process in which humans and robots work together to assemble parts or complete a manufacturing task, combining the precision and strength of robots with the flexibility and decision-making abilities of humans. ACROBA has developed two collaborative manufacturing pilot lines in the field of electric components assembly.
Electronic Elements Assembly for Electric Motors Manufacturing (Romania)
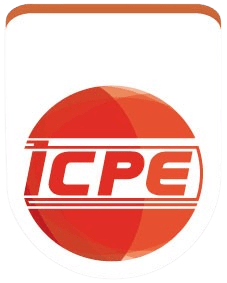
ICPE is a Romanian medium enterprise covering a wide range of topics in the field of electric engineering in both production and research. ICPE produces a wide range of motors/generators for many applications ranging from industrial automation, defense, EV traction and special applications.
Electric motors manufacturing involves the assembly of distinct types of electric components with multiple design variations. The variability of the production (with multiple raw materials) is the main challenge faced by ICPE. So far, ICPE’s production entirely relies on manual labour, except for CNC machining. ICPE use case focuses on two key processes in motor manufacturing :
- the winding process, which involves winding copper wire around the stator teeth.
- the bonding process, applied to the rotor’s production by bonding specific magnets into place.
The introduction of robotic systems into these processes has multiple advantages:
- improvement of employees work quality
- increased flexibility of the manufacturing process
- improvement of final product quality and consistency
- reduction of operating and labour costs
- reduction of material waste.
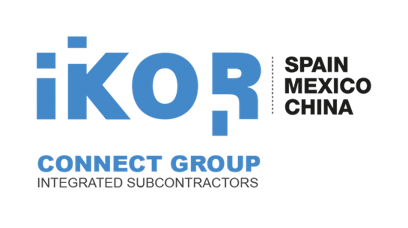
IKOR provides a total service for the design and manufacturing of electronic circuits (EMS), including supply chain solutions for world-leading industrial and technological companies.
The variability of their manufacturing services, addressing to different sectors such as automotive, medical, industrial or home appliances, and the multiplicity of raw materials in the Printed Circuit Boards and electronic components, are the main challenges currently faced in their production.
The pilot case focuses on the assembly of small electronic components or PTHs (Pin-Through-Hole) on electronic boards or PCBs (Printed Circuit Board).
Currently, this process is done manually in a line with 3-4 operators in which each operator is in charge of a subset of electronic components to be assembled.
The goal of the use case is to integrate a collaborative robotic system into the line, which will be in charge of another subset of electronic components, decreasing the load of the operators.
Therefore, both human and robot will coexist in the same workspace and they will carry out parallel but inter-related assembly tasks.
The integration of ACROBA increases the output quality while reducing damaged and missing parts, and interruptions in the production.